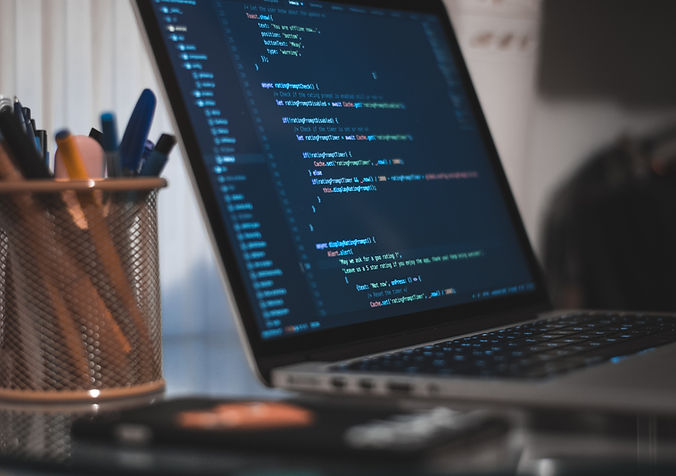
Lean Manufacturing
Lean Manufacturing is a production philosophy that aims to maximize value for customers while minimizing waste. Key aspects include.
​
a) Continuous Improvement of Process.
b) Elimination of non-value-adding activities.
c) Just-In-Time production.
d) Employee Empowerment and Involvement.
e) ​Efficient use of resources.​
f) Streamlined workflows and reduced inventories.
h) Reduction of variabilities and defects.
i) Focus on (Internal) customer needs.
(Never be fearful of modifying or optimizing aging bookshelf lean philosophies - Bespoke Lean) ​
Lean Manufacturing
The door to Change.
"Cutting the fat out of lean" Understanding the effects of commercialism on waste and convolution:
A perspective look commercializing the business of waste.